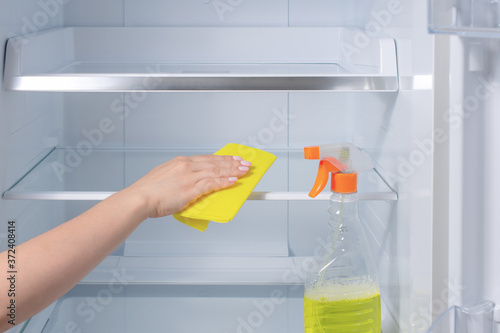
Freezer rooms, cold rooms, and controlled ambient stores represent a considerable financial investment and should, with proper maintenance, last for 20 or 30 years. However, the damage and degradation of freezing and cooling equipment can result in poor performance and increased running costs. Common problems include worn out insulation (especially for freezers), door hinges, and door seals, or cracks in the internal or external covering. Condensation on the outside and the presence of ice is an indication of a malfunctioning refrigeration system. When this occurs, the equipment should be repaired or replaced. Another indication of insulation degradation is an excessively long compressor duty cycle; the cooling equipment runs continuously with the interior never reaching the set point.
The following maintenance checklist can help companies prolong the useful life of their refrigeration equipment.
Condensers:
- Clean them regularly, especially air-cooled types
- The frequency of cleaning depends on the condenser location and its surrounding environment
- Check fan/pump motors are functioning
- Check fans are not loose on motors
Compressors:
- Carry out standard maintenance if required
- Recover oil and recharge compressors as necessary (ammonia systems)
Air coolers:
- Clean them regularly
- Check the defrost (where necessary) is working correctly
- Check the defrost control allows the optimum time for defrosting
- Check fan/pump motors are functioning
- Check fans are not loose on motors
Liquid chillers:
- Check water pump operation.
Liquid line filter drier:
- Check for blockage and replace if necessary.
Refrigerant charge:
- Check liquid level in the receiver or check for bubbling in the liquid line sight glass
- Check for leaks all-round the system and repair (this is required under EU 'F-gas' regulations on the use of fluorinated greenhouse gases)
Control:
- Ensure the discharge pressure is as low as possible; in particular, check that head pressure control settings are not too high
- Check that the suction pressure is as high as possible
- Check cold room/process temperature set points; they should not be lower than required
- Check superheat setting of expansion valves and adjust if necessary
Insulation:
- Replace suction line insulation if necessary
- Replace chilled liquid line insulation if necessary
- Repair or replace cold store insulation if necessary
Cold store doors:
- Ensure doors are not left open unnecessarily
- Repair or replace door seals if necessary
- Repair or replace strip curtains if necessary
- Repair or replace air curtain if necessary
Ice build-up:
- If condensate pipes are iced-up, applying gentle heat will help to defrost
- Integral defrosting elements should work correctly
- Ice build-up on evaporators indicates to poor heat exchange
- Light ice build-up can be removed with a brush, but heavy ice has to be removed as described in manufacturer guidelines
- In order to avoid damage, sharp objects should never be used for de-icing
- The Retail Code of Conduct includes information on service and maintenance of cooling systems